The welding of motor windings determines the lifetime of the motor
Motor winding welding is a key production process in the motor production process, such as the welding of the winding main line to the main line, the welding of the main line to the lead wire, the welding of the copper bar rotor guide bar to the end ring, and so on. All of these links will directly affect the reliability and quality level of the motor operation. Motors of different types or sizes often involve unique welding processes and cannot be treated simply and equally. Today, Ms. Shen will talk to everyone about common winding welding methods.
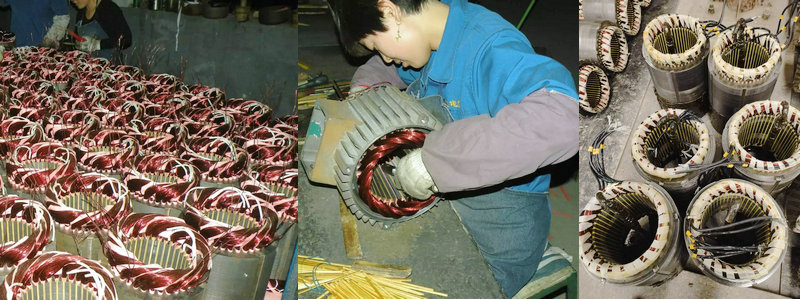
Common Welding Methods for Motor Windings:
Silver brazing (gas welding)
This welding method is suitable for occasions with high working current, high temperature, and high reliability requirements, and is also the welding method adopted by most motor manufacturers. The welding equipment is an acetylene oxygen welding gun. When welding, to prevent the insulation of the motor wire near the wire head from being scalded, asbestos rope dipped in water should be wrapped around the wire head. At the same time, it is necessary to prevent solder and flux from flowing into the gaps of the coil, causing insulation damage and short circuits.
Soldering
Tin soldering is most commonly used due to its convenient operation and firm welding points, but its working temperature is relatively low. The commonly used soldering methods include soldering iron and pouring tin. When the number of welding wire ends is large, the method of pouring tin can be used. Due to the limitation of low melting point of solder tin, it is only used on small motors and motor windings with low temperature rise.
arc welding
When the wires of the winding are thin, arc welding can be used for welding. The characteristic of electric arc welding is that it does not require flux, which is fast and convenient. However, when multiple parallel connections are made and there are many wire ends, if the operation is not proficient, it is easy to miss welding or the welding is not firm.
Copper aluminum welding oxygen gas welding
When welding, first coat the connecting part of the copper wire or copper lead with tin, and then twist the cleaned aluminum wire onto the copper wire, making the aluminum wire slightly higher than the copper wire. Apply another layer of aluminum welding powder and melt the aluminum wire with a neutral flame of gas welding, allowing the aluminum to fuse at the top of the copper, forming a spherical solder joint. This method is used in the welding process between the main line and the lead wire in many motor factories.
Argon arc welding
Argon arc welding is a welding technique based on the principle of ordinary arc welding, which uses argon gas to protect metal welding materials. Through high current, the welding material is melted into a liquid state on the welded substrate to form a molten pool, achieving metallurgical bonding between the welded metal and the welding material. Due to the continuous supply of argon gas during high-temperature melting welding, the welding material cannot come into contact with oxygen in the air, thereby preventing oxidation of the welding material. This welding has played a good role in the welding quality of multi turn windings.
hi-frequency induction brazing
Induction brazing is the process of placing metal workpieces (usually red copper) that need to be welded into an induction coil, passing high-frequency alternating current to generate an induction electromagnetic field, coupling it with the surface of the workpiece to generate an induction electromotive force, and forming an induction eddy current on the metal surface. By relying on the eddy current generated on the metal surface to generate heat, welding powder is usually applied to the welding area, and welding can be completed when the workpiece reaches the melting temperature of the brazing material, Induction brazing is currently the cleanest and environmentally friendly heating welding method in the world. This type of welding is widely used in copper bar rotors because it involves simultaneous operation of several welding points, resulting in good consistency of process parameters and effective deformation of the welding points. It is a good process in terms of efficiency, reliability, and aesthetics. However, due to the relatively high equipment cost and the corresponding induction coil cost, not every manufacturer adopts this welding technology.
Medium frequency induction brazing
The medium frequency induction brazing equipment is used to assemble surface cleaned workpieces together in a lap joint pattern, and place the brazing material near or between the joint gaps.
Medium frequency induction brazing equipment can replace outdated heating methods such as oxygen acetylene heating, coal oven heating, and box electric furnace heating for brazing and quenching heat treatment. It can greatly improve product quality, effectively save electricity, and improve labor conditions. When the workpiece and brazing material are heated to a temperature slightly higher than the melting point of the brazing material, the brazing material melts (the workpiece is not melted) and is sucked in and filled with the gap between the solid workpiece through capillary action. The liquid brazing material and the workpiece metal diffuse and dissolve each other, forming a brazing joint after cooling. The characteristics of medium frequency induction brazing equipment: 1. Due to the principle of electromagnetic induction heating, the heat is generated by the workpiece itself. This heating method has fast heating speed, minimal oxidation, high heating efficiency, and good process repeatability. The metal surface only has slight discoloration, and slight polishing can restore mirror brightness to the surface, effectively achieving constant and consistent material properties. 2. Heating is uniform, with high temperature control accuracy. Heating is uniform, ensuring a small temperature difference between the heating core and the surface. The temperature control system can accurately control the temperature, ensuring the repeated accuracy of the product.
Medium frequency induction brazing is widely used in the welding of bare copper bar rotor guide bars. This welding method requires strict requirements for the cutting, forming, and related head cover shape of the guide bars, otherwise the welding effect will be greatly reduced.
Based on the above information, each motor manufacturer should conduct a comprehensive evaluation based on their own equipment and product characteristics, but welding quality reliability is a key technology in production and manufacturing.